Cooling towers are comprised of many different components, all of which differ depending on the use and function of your tower. One element that can vary is the power transmission technology used to power the internal fans.
For towers with a motor sized 11 to 30kw, the most common way to transmit power is by a gearbox or belt drive. Many people are confused when it comes to choosing between a gearbox and belt drives. There are many things you must consider, as it all depends on your situation and needs. But the right selection of components should create a good balance of initial cost and operating costs.
Since 2002, Marley Flow Control has been the industry leader in all things regarding cooling towers. We are an Australian-owned and operated brand that offers a high level of expertise and a large range of products that are ready to order. Marley Flow Control’s wealth of knowledge has allowed us to work with some of the country’s largest businesses and corporations.
So gearbox vs belt drive – which one should you choose for your cooling tower? Read on to learn more.
What is a cooling tower?
A cooling tower is a specialised device that discharges heat waste into the atmosphere. This process is done by drawing cool air over the surface of the water. Small amounts of water then evaporate, which lowers the temperature of the water running through the tower.
Cooling towers are used to lower the temperature of the circulating hot water from the condenser or any other heat exchanger. The cooled down water is then ready to be pumped around again back to the heat exchangers.
What is a gearbox?
As simple as it sounds, a gearbox is just that – a box full of gears. These gears mesh together to produce a reduction ratio of input to output speed. This gearbox is much the same as one in your car – except in a cooling tower, the gear ratio is fixed, not shifted, depending on the manufactures determination of optimum fan speed.
What is a belt drive?
A belt drive refers to the black ‘ribbon’ or ‘belt’ that you find around pulleys. Belt drives are often wrapped around pulleys of two different sizes. When the belt starts to spin the pulleys into motion, the mechanism begins to move. Once at full motor speed, the fan spins at a speed according to relative pulley diameters in the same way the gear ratio is described above.
What are gearboxes and belt drives used for?
To function properly, a cooling tower needs sufficient airflow throughout its structure. This airflow cools the water within the tower, so it is crucial that there is always a strong air supply.
Fans are the most effective and reliable way to create airflow. Unfortunately, the fans can’t operate without help – they need an electric motor to produce constant airflow.
The motor cannot be connected to the fan directly – that would cause the fans to run too fast. One, therefore, needs something between the fan and the motor to reduce the fan’s speed.
This is where gearboxes and belt drives come in. Installed between the fan and the motor, they are used to reduce, control and maintain the speed of the fans.
Gearbox features
Higher reliability
Being specifically designed for cooling towers, gearboxes are high quality and less prone to break down. It’s crucial that the device used to power your tower’s fans are reliable – if the fans stop working, then the tower cannot perform its function to its full potential capacity. Your facility will have to shut down temporarily while the problem is resolved.
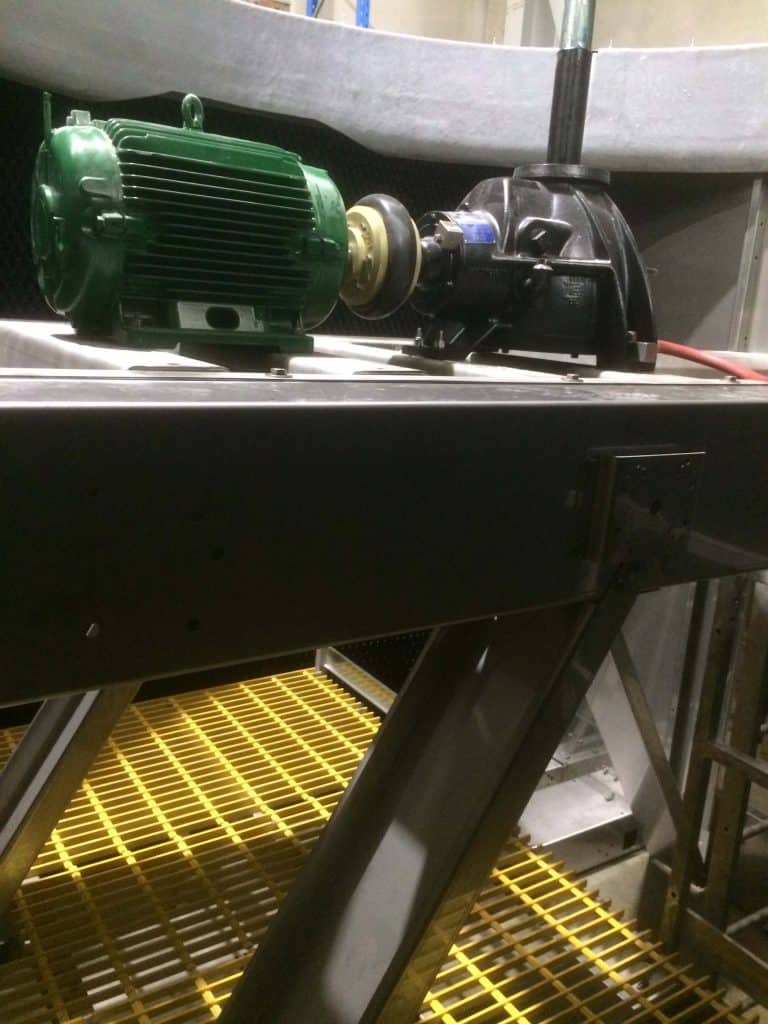
In the rare case that your gearbox does need repairing, you won’t need to shut down your facility. Gearboxes allow for motors to be installed on the outside of your tower, rather than inside it. You will be able to attend to your gearbox without having to go inside your cooling tower, or shutting down production.
Gearboxes also have a long operation span, so they will last as long as the life of your cooling tower.
Low maintenance
Like all your facility’s machines, gearboxes need regular monitoring to ensure that they are operating efficiently. But thanks to its large oil volume, gearboxes only require an oil change once every five years.
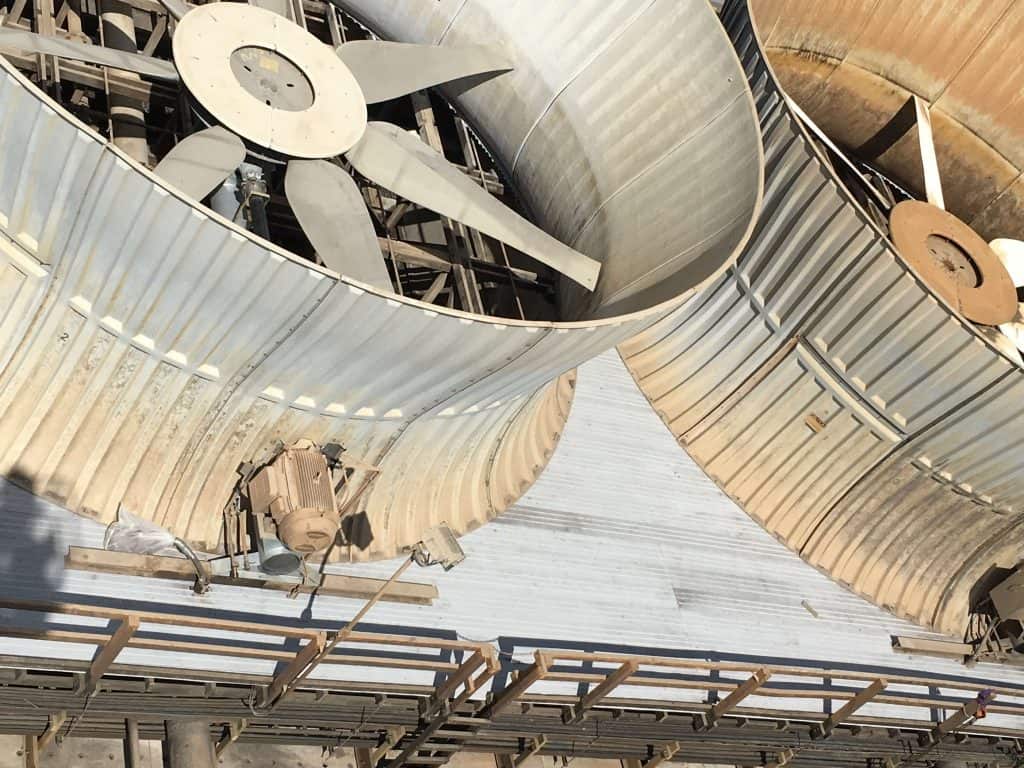
Unlike belt drives, these gearboxes are designed solely for the operation and use of cooling towers. As a result, they have large oil volume and a big surface area for cooling. They also don’t need any specialised device or process for cooling itself. This means less maintenance for a more efficiently running tower.
Belt drive features
High maintenance
In contrast to gearboxes, belt drives are suitable for many machines with different operations. They are not specially designed for cooling towers and therefore need more maintenance.
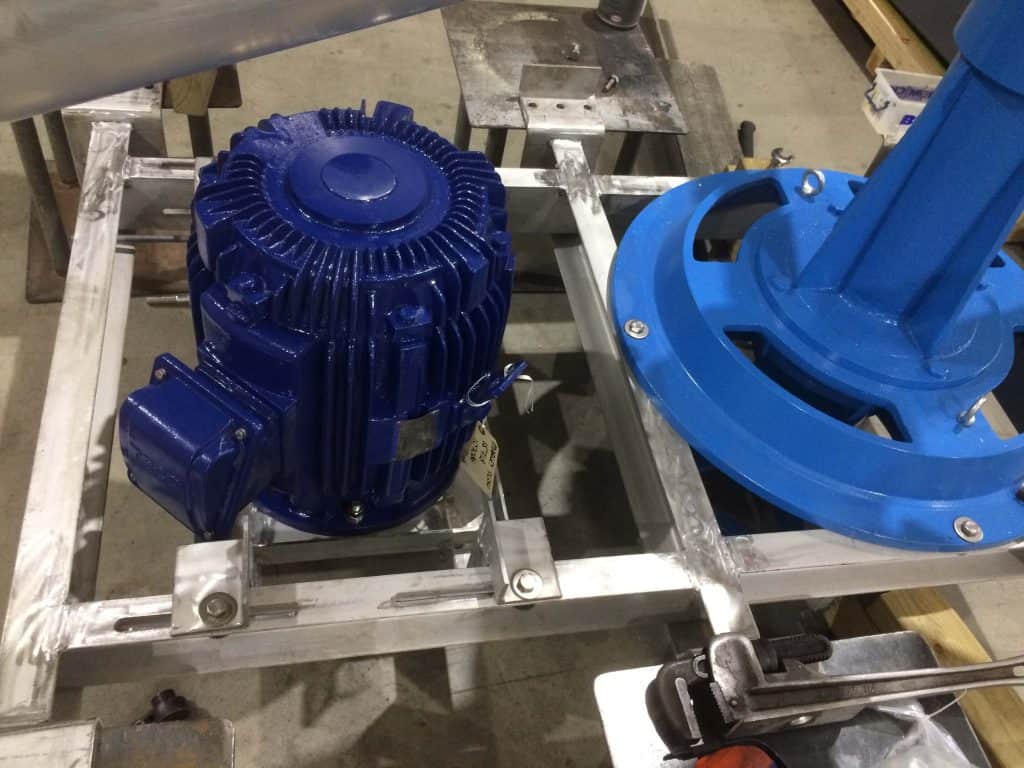
Belt drives are a consumable item, meaning that they wear out and need replacing every 6-12 months. The belts can loosen and need regular tightening. The ball bearings in the shaft that turns the fan can fail. Once this happens, it’s almost impossible to repair.
Can be noisy
When the belt begins to slip from the pulleys, the drive will start to squeak, making an irritating noise. This can be troublesome for facilities in urban areas or for those with sensitive neighbours.
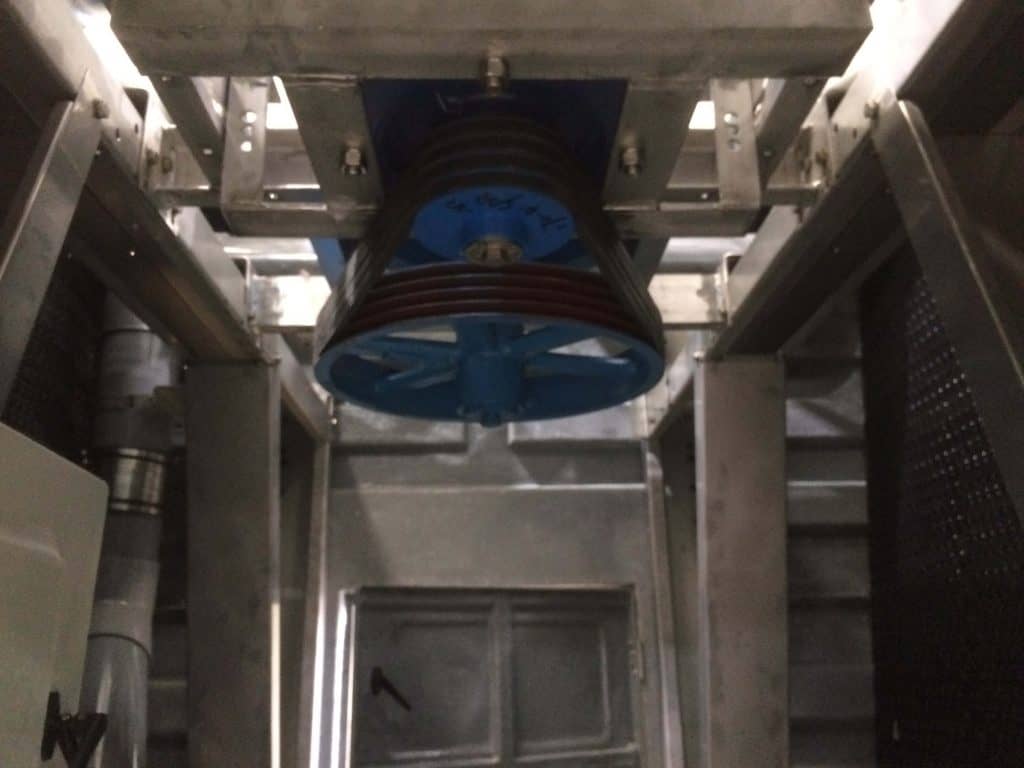
As the belt drive is inside the tower itself, the squeaking belt can only be repaired by shutting down the facility and entering the tower. This can increase stress, time, and money.
What is the cost difference?
Belt drives are simple mechanisms that are readily available. They are very cost-effective initially, but thanks to the constant replacing and maintenance, can be quite costly long term. The yearly total of belt drive maintenance is approximately $2,300, or $11,900 over five years.
The price of gearboxes depends on the size of your tower. The bigger your tower, the less expensive the upgrade to a gearbox will be. For example, small towers may have to pay a few thousand dollars for a gearbox, while a larger tower may only spend a few hundred.
The long term cost of a gearbox, however, is far less than belt drives. Thanks to their high reliability, gearboxes rarely ever need replacing or repairing. The yearly total of gearbox maintenance is approximately $624, or $4,270 over five years.
Find out how we can use our engineering experience to help find the right solution for your business needs. Contact us here for a free quote.